一,项目说明
大同电力机车有限责任公司(以下简称同车公司)隶属于中国北方机车车辆工业集团公司,企业始建于1954年,是国家“一五”期间重点建设的156个大型国有企业之一,目前公司共拥有各类机械动力设备3000余台,员工总数7000余人,是我国铁路干线电力机车主要研发制造基地和各种机车车辆配件定点生产厂家,被认定为山西省高新技术企业,拥有国家级企业技术中心。
作为国家机车行业重点扶持单位,最近几年同车公司驶入快速发展的轨道,各项指标持续翻番增长。为确保公司良好的可持续性发展,公司领导高度重视信息化建设,并确定了建立数字化同车公司的战略方针,重点打造全新的数字化设计和数字化制造的同车公司。截至目前为止,公司已经初步完成设计及管理系统的数字化,成功实施了CAD/CAM、PDM、ERP、OA等系统,这些系统在各项新产品中发挥了重要作用,成为公司高效率、高质量产品研发的重要保障手段。
在数字化制造方面,公司最近几年陆续引进50余台先进的数控设备,这些设备承担了许多关重件的生产任务,并构成了数字化制造的硬件基础。但在程序传输、程序编辑与仿真、数控程序的管理、机床数据采集等方面还存在一些不足,制约着数控设备的最大生产能力的发挥,离公司规划的数字化制造的目标还相去甚远。具体表现如下:
1) 程序通讯方面:各机床都是单机通讯,通讯软件相互不兼容,传输效率低,每台数控机床成为一个事实上的信息化孤岛。
2) 程序管理方面:程序没有集中管理,没有签署流程管理、没有严格的权限管理和版本管理,没有日志管理功能,出了问题无法进行追溯问题的根源,不符合ISO9001要求。
3) 程序编辑与验证方面:编程员缺少数控程序数值处理、程序模拟仿真、程序版本比较等数控编程专用软件,编程效率低,程序容易出错。操作工无方便的程序轨迹预演工具,操作存在一定的盲目性。
4) 机床监控方面:由于工厂的管理部门或管理系统不能及时得到生产设备的实时生产状况,因而不能做出科学的生产管理计划及措施,极大地影响了车间生产效能的发挥。
5) 刀具管理方面:对规格多、数量大、使用频繁、损耗率高的刀具缺少行之有效的管理手段,直接影响到企业的生产效率和制造成本。
针对以上情况,同车公司决定将信息化进一步延伸到数控车间,完全打通设计——制造的信息化瓶颈。基于近几年的DNC技术热潮,结合公司实际情况,提出了具有同车公司特色的分布式制造集成系统(Distributed Manufacturing Integration System),简称(DMIS系统),用一台计算机对所有数控机床的程序传输、程序数据库管理、机床监控以及刀具信息进行集中管理,本系统作为数字化车间建设的第一步,与以后实施的MES制造执行系统,将共同组建全面的数字化车间。
二,方案选型
目前国内做DNC的厂商众多,既有国外的产品,也有国内自主开发的产品,如何选择一家完全能真正地实现以上目标的合作伙伴,同车公司专门组织了多学科、多部门的项目小组,对各供应商的方案组成、技术细节、实施案例、实施力量等进行了全方位的认真调研与细致评估。重点考察以下几个方面:
1)方案的成熟性。因本项目是涉及计算机、数控加工、网络、刀具管理等多学科技术于一体的工程,为确保整个项目的成功实施,所选方案必须是一套成熟的产品,系统应具有良好的灵活性、兼容性、可扩展性与高可靠性,并在国内外有众多成功用户,尽量不选取刚刚开发或还不完善的系统。
2)方案齐全性,且具有良好的可扩展性。所选方案应该完全满足项目的整体要求,并且各模块之间信息是共享的、完全集成的,软件供应商最好具有MES系统,以便该系统的进一步扩展。
3)技术先进性与易用性。除了系统要具有最先进的技术指标以外,还应该具有最大程度的易用性,比如远程比较功能,操作工不用离开机床,就可以直接将机床内的程序和服务器的程序进行比较,并将比较结果显示在机床上。
4)本地实施力量强、经验丰富,并具有与其他系统进行集成的能力。数控设备动辄上百万,真正的实施远非几个菜单设置那么简单,需要的是工程师丰富的现场实施经验。如果是国外产品,代理商还应具有二次开发能力,可根据我公司的实际需要进行一些功能的定制开发,并能与PDM等其他管理系统的集成等,而不是一个信息化孤岛。
最后北京兰光创新科技有限公司提供的整体解决方案在各方面均有突出表现,脱颖而出,成为一致选择从而顺利中标。
三,方案组成
兰光 DNC 提供了一整套功能齐全、性能可靠的整体解决方案。 兰光创新系统软件部分由机床联网通讯、 数控程序的编辑与仿真、数控程序的数据库管理、机床监控与数据采集系统四部分组成,这四部分是个有机的整体,以及Smart Crib刀具管理系统,共同构成同车公司的分布式制造集成系统,简称DMIS系统。
在该系统中,我们以DNC-Pro为信息网络平台,以NCBase为程序管理核心,以MDC-Pro为信息采集关键技术点,以EDIT-Pro为编辑仿真手段,并通过Smart Crib 刀具管理系统实现对各车间刀具的管理,针对数控车间的特点,全面打通程序编辑、仿真、管理、传输、监控、刀具、机床等各环节,形成具有同车公司特色的数控车间数字化解决方案。
1,兰光 DNC-Pro机床联网系统
兰光 DNC-Pro系统,主要实现数控设备的全部联网与远程通讯等功能,主要功能如下:
1.1 网络通讯
通过RS232接口或机床网口,一台服务器可实现对256台数控设备的双向并发通讯。
1.2 远程控制
远程查询,在机床控制面板上,机床操作员能够直接查询DNC服务器上的程序清单、程序大小、编程日期等信息。
远程请求,机床操作员直接在机床控制面板上可以下载所需要的加工程序。
远程自动接收,程序上传时,服务器能够自动接收、自动命名、自动保存数控程序,服务器无须专人值守。
远程比较,在机床控制面板上可以直接将机床内的程序和服务器的程序进行比较,并将比较结果显示在机床上。
1.3 在线加工
提供稳定可靠的在线加工能力,只要机床具有在线加工功能,DNC-Pro都可方便可靠地实现在线加工。
智能断点续传,DNC-Pro可以从程序的任意行、任意换刀处实现程序的断点续传。
1.4 传输透明
通过远程网络配置和管理,网络上的任意客户机可以实现对任一通讯端口的监控。
多重校验机制,程序每次传输都有成功或失败报告,程序传输智能化、透明化。
1.5 强化管理
强制上传功能,可以做到操作者在下载一个新的程序前必须把机床内程序发回服务器,确保服务器上永远保存最新版本的程序,便于规范化管理。
1.6 其他辅助功能
DNC-Pro具有强大的前处理和后处理能力。针对不同的机床控制系统,在传输过程中就可以对程序的特殊字符进行替换、增加、删除等数据处理。
大程序智能分段功能,一些老系统内存空间有限,大程序放不下,通过自动智能分段传输功能,可省去人为的删截程序所造成的失误和不便。
支持长文件名,完全支持256位文件名,能实现程序名与文件名的自动转换。
可以传输刀具参数、备份机床参数,便于机床出现故障时恢复使用。
2,兰光 NCBASE程序管理系统
兰光NCBase V5是一套完全基于PDM理念并充分考虑到数控加工行业特点而开发数控程序专业管理系统。它具有以下功能:
2.1 流程及权限控制
完全支持编制、校对、审核、批准等流程,用户并可以根据企业实际情况进行流程的自定义。
强大的角色管理功能,如编程员、编程主管、检验员、技术主任等,对加工程序进行可靠的权限管理,不同的人员设置不同的权限,确保程序安全可靠。
具有完善的任务管理、提醒、更改、委托、追回与任务作废等功能。
2.2 良好的文件兼容性
内嵌的智能浏览器,可对各种文本、图片、Autocad、CATIA、PRO/E、UG等各种数据文件,并对CATIA等三维图形文件能直接进行缩放、旋转、平移、剖切。
2.3 程序信息自动提取
自动产生刀具清单文件,包括刀具名称、几何参数等,并自动关联到该程序上。
程序信息自动提取功能,比如系统对程序的图号、编程员、机床等信息自动进行提取。
2.4 强大的出入库管理
程序下发受程序状态控制,完全避免未审核程序被误调到机床。
程序入库具有严格的版本比较等入库处理,从根本上保证了入库程序的正确性。
2.5 先进的数据库技术设计
采用先进的服务器/客户端架构,用户在客户端具有与服务器完全一样的功能,操作方便。
数据全部集中存储在Oracle 的数据服务器上, 完全避免了共享文件夹等系统安全问题,系统无网络安全、病毒攻击、人为破坏等潜在危险。
智能模糊查询功能,可以让你快速找到您要查找的程序。
具有完善的版本管理功能,可自动跟踪、记录程序文件的所有变更,允许用户比较/恢复老版本。
自动产生程序管理记录,包括创建、修改、检验、批准、删除等事件的时间及人员,使程序具有可追溯性,完全符合ISO9001管理标准。
机床负荷统计功能,自动生成编程员、操作员、每台机床的程序负荷及程序进度统计报告。并以醒目直观的柱图、饼图等形式表现出来。
系统具有可靠的定时自动备份与智能恢复功能。
3 EDIT-Pro程序编辑与仿真系统
Edit -Pro 是兰光创新公司专为数控编程而设计的专业软件,它具有强大而实用的数控编辑功能、文件的智能比较、刀位轨迹的三维模拟等功能。其主要功能简述如下:
3.1 程序编辑
行号的重排、空格插入、字符大小写的转换等数控编程专用工具,可以极大地提高工程师的编程效率。
数据处理功能可以方便地实现对各轴数据的运算,迅速完成程序缩放、旋转、镜像以及主轴转速、切削进给的动态调整等数控程序专用功能。
强大的固定循环/宏定义功能,用户可以更快速地增加/编辑复杂循环。
可自动对程序进行海德汉格式与ISO格式之间的相互转换。
3.2 文件比较
智能文件比较功能,很轻松地标示出两个文件的数据差异、错行、漏行,并可以马上修改。
3.3 程序仿真
强大的三维刀位轨迹和实体的动态模拟功能,可对数控车、数控铣程序进行方便、高效的轨迹仿真,令错误暴露无遗,有效避免程序错误。
刀位轨迹和实体的正反运行,自由的缩放、旋转和移动。
程序与刀位轨迹的的动态交互分析,可方便查看任意程序对应的刀位以及任意刀位对应的程序行;并可以进行图形测量。

程序仿真
文件智能比较
3.4 程序统计
快速统计加工时间和每把刀具使用时间,便于制定科学的生产计划和刀具更换或刃磨计划。
方便实用的加工范围统计功能,可以快速判定程序是否有超程问题。
4 兰光 MDC-Pro机床监控与数据采集系统
MDC-Pro提供强大的机床数据采集功能和实时的分析能力,可以为我们提供包括实时的机床利用率(OEE)等各种分析统计功能,从而为科学安排生产计划、采取正确措施提供准确、可靠的数据基础。对高端机床,MDC-Pro可实现如下功能:
4.1 机床信息实时采集功能
可从网络上的任何PC机监控所有的机床状态
全功能的机床状态电子看板
机床是联网状态还是脱机状态?
机床是处于加工、停机还是故障中?
什么产品正在生产中?
机床上正在加工哪个程序?
已经生产了多少件工件?
机床报警信息
实时的主轴进给速度和主轴转速
刀具位置信息,如绝对位置、相对位置、机械位置、剩余移动量等
4.2 . 丰富的统计报告
MDC-Pro 提供超过丰富的统计报告模板,可方便、整齐地显示需要的各种数据,可准确知道每台机床出现了什么情况及生产计划完成情况。如:
每个工件加工时间
每个操作者或每班组加工的工件数量
机床开机时间
机床停机时间
机床故障时间
机床运行时间
操作工的效率
机床利用率(OEE)
5 Smart Crib刀具管理系统
Smart Crib 是北京兰光创新科技有限公司集国外先进的刀具管理理念与国内用户的具体需要相结合而研制开发的刀具管理平台。 Smart Crib 刀具管理系统具有完善的数据库管理功能,能够非常灵活、高效地对不同生产厂家、不同类型的刀具进行多库房管理,规范的出入库操作,智能的组合刀具拆装,丰富的库存统计等各种强大的功能。 Smart Crib 刀具管理系统可以使我们轻松获得刀具的最优资源配置,有效地降低生产中的刀具成本,并在最短时间内完成刀具准备,明显地提高机床的利用率。
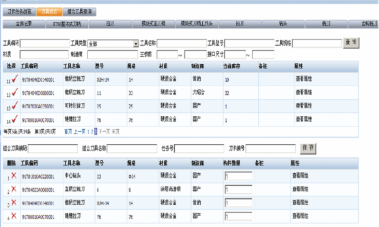
Smart Crib刀具管理系统界面
5.1 主要功能
采用目前前沿的 B/S 架构,充分利用 Internet 技术,实现网络内刀具信息共享。
多级权限管理,系统管理员、刀具管理员、技术人员、机床操作人员,不同的人员具有不同的权限,系统使用友好方便。
多库房、多车间管理。
基本刀具管理,如各类刀具定义参数,刀具出入库管理;
组合刀具管理,包括组合刀具组装、借出、改装、拆卸、多功能查询;
贵重刀具管理,贵重刀具新购、出入库、打磨维修、报损、维修入库,刀具寿命管理;
刀柄管理,如刀柄新购、出入库、报损管理、多功能查询等;
附件管理,附件新购、出入库、报损管理、多功能查询;
库房预警、自动订货功能;刀具积压预警、库存不足提前预警并自动产生刀具订购报表。
报表管理(丰富的各类报表统计功能,如刀具库存、刀具成本、附件类报表、刀柄类报表、贵重刀具类报表);
四,各模块间的信息流及关系
同车公司本着总体布局、分步实施的原则,建成一个与其他系统高度集成的数字化车间,有计划、有步骤地完成与其他系统集成,而不是一个数字化孤岛,逐步实现了与其他系统的有机集成。
1. 与CAD/CAM系统的集成。
DNC 系统在加载程序时可自动获取数控程序中的零部件加工信息,比如刀具清单、加工时间、零件号、图号、工序号等相关信息,这些信息自动进入NCBASE程序管理系统。 NCBASE可对CAM的三维模型进行关联管理,可以直接浏览各类WORD、PDF等工艺文件,以及CATIA、UG、PRO/E等图形文件,并对CATIA等三维图形能直接进行缩放、旋转、平移。
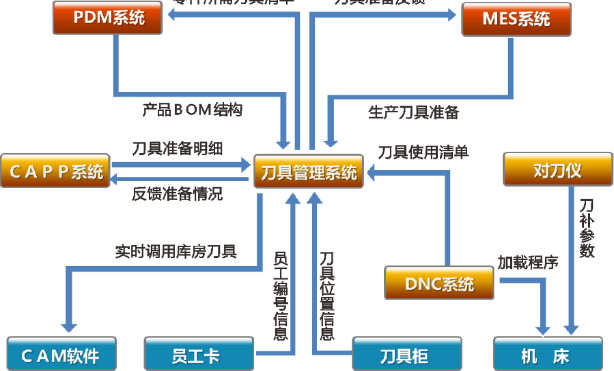
各模块的数据流集成关系
2. 与PDM系统进行集成。
数控程序经过DNC系统进行传输、机床调试、审批流程而到固化定型阶段后,可自动进入PDM进行管理,确保PDM中数据的完整性,同时由PDM对数控程序进行备份管理。定型程序再次生产时,由PDM将加工程序、刀具清单、工艺文件等下发到DNC系统,由DNC系统传输至机床实现加工生产。
3. 与MES/ERP系统进行集成。
可将ERP/MES制定的生产计划,特别是数控加工计划指令下发到DNC系统,DNC系统根据该计划指令进行程序的顺序生产。
机床监控系统将程序完工情况反馈给ERP/MES系统,后者根据实时的生产状态动态调整生产计划,从而使生产计划更科学、更准确,全面实现生产计划的闭环管理。
五,实施效果
通过在四个机加车间成功实施DMIS系统后,同车公司有效地达到了如下目标:
1. 实现工厂的完全网络化管理,彻底消除机床信息孤岛。构建基于以太网的DNC网络,彻底改变以前数控机床的单机通讯方式,全面实现机床的集中管理与控制,机床由以前的信息孤岛转变为整个工厂的信息节点,实现数控机床的完全网络化管理。
2. 程序管理更科学规范。DMIS系统完善的程序签署流程、准确的权限管理、方便的版本管理以及良好的可追溯性,实现对NC程序全生命周期的跟踪管理,提高NC程序的规范化管理水平,让编程员、操作员在正确的时间轻松地处理正确的工作,生产出正确的产品,完全符合企业ISO9000认证及管理的需求。
3. 明显提高机床利用率,减少机床辅助时间。DMIS系统方便、可靠、全自动的程序传输功能,快速、高效的程序编辑功能,准确、直观的程序模拟仿真功能,程序工艺文件的关联管理与快速查找功能,都可以将程序编辑、仿真、管理等生产辅助任务在计算机端完成快速高效地完成,可最大程度地提高机床的有效利用率。
4. 产品质量进一步提高,明显降低产品废品率。专业的程序模拟仿真可把程序错误最大程度地消除在虚拟环境中,确保程序的正确性;规范严谨的程序管理,可从根本上避免程序误调用的可能,从而完全避免因程序错误而出现批次报废的情况;传输过程中的多重检验机制,确保程序的传输更加安全可靠。兰光DNC可从最大程度上避免程序错误,从管理手段与措施上使产品质量有了根本的保障。
5. 明显降低相关人员劳动强度。强大的版本比较、程序仿真、数据处理、程序管理、全自动传输等功能,可将编程员从枯燥的程序编辑、检查、调试、传输中解脱出来,可更轻松、高效地从事更多有创造性的工作。服务器端无人职守、机床端全自动远程传输,操作者不用离开机床就能完成程序的远程列表、远程调用、远程比较、远程上传等全部工作,明显降低了操作者因程序传输跑来跑去的辛苦。
6. 车间现场更加整洁,符合6S车间现场管理要求。因DMIS系统实现了程序的集中管理与集中传输,车间现场不再需要大量的台式计算机及桌椅板凳,取而代之的是少量美观大方的现场触摸屏,整个车间显得更整洁、简练、美观,更符合车间6S管理的要求。
7. 以DMIS系统为主线,车间人员分工明确,职责清晰,初步实现车间的无纸化生产:
1) 机床操作者,通过简便的方式实现数控程序的远程调用,并通过现场触摸屏实现数控程序、刀具清单、三维模型、加工工艺等相关文档的调阅,以及程序的三维动态模拟仿真,操作者也可利用快速统计功能,准确地预测程序加工时间和刀具更换时间。
2) 工程师,在自己的计算机上以客户端的方式,完成数控程序的编辑仿真,流程签署、程序及关联文件管理、程序版本管理、程序入库、程序下发等功能。
3) 刀具管理员,全面实现各类刀具、刀柄的出入库管理、 组合刀具的智能拆装、刀具库存、刀具成本的自动统计功能。
4) 系统管理员,实现对系统的流程定义、角色定义、权限划分、数据库的备份与恢复等管理工作。
5) 管理人员,通过DNC系统可查看并自动统计机床、程序员、操作者的程序负荷、程序的流程状态以及机床的实时状态。
8. 实现对高端机床实时的数据采集与分析功能。通过强大的机床数据采集功能和实时的分析能力,可以为公司管理者提供包括实时的全部机床利用率(OEE)等各种分析统计功能,从而为科学安排生产计划、采取正确措施提供准确、可靠的数据基础。
9. 通过DMIS系统与PDM等其他管理系统的集成,将车间制造资源与产品设计资源有机整合在一起,从而实现整个工厂全面的数字化生产奠定良好的基础。